Design and Optimization of Front Wheel Hub for BAJA SAE
- Chaitanya Mehta
- Jan 24, 2020
- 6 min read
Updated: Mar 28, 2021
Function of the front wheel hub is to bear/ transmit road loads to the suspension system and chassis through knuckle, support and position the brake rotor in place, position stud bolts on which the wheel will be mounted through wheel rim.
These are our constraints, and our goal is to minimize the weight and make a robust wheel hub. Usually wheel hub has four arms - it supports the wheel rigidly with each arm helping to counter lateral forces and moments that may arise during the operation.
Generally, a wheel hub has four flanges. Some teams in Formula Student, as well as BAJA, has ventured to go with 3 flanges, but if we don't want to mess up with our wheel rims, it is better to go ahead with traditional 4 flanges.
Before designing any wheel assembly, The first thing I do is: Sketching out and knowing all our constraints. Here we have the following dimensional constraints from the components of wheel assembly:
1. Stud Bolts: Munting Hole size and pitch circle diameter
2. Brake Rotor: Pitch Circle Diameter & mounting hole diameter, positioning from the wheel rim. Positioning from the wheel rim is important as the brake calliper will be positioned on the brake rotor, and it will have to maintain appropriate clearance from wheel rim as well as rotating wheel hub.
3. Hub Bearings: Bore Diameter, Thickness positioning of Hub bearings
4. Circlips (retaining rings): Groove size and clearances of the circlip. Following Resources can be useful for the selection of retaining:
As the wheel hub is designed symmetrically to prevent balancing issues when in rotation, we can utilize shaft/revolve function for designing the hub. Then subsequently we can use Pad- pocket, chamfer, fillets to make other features. First, on the base sketch, We will mark four holes for the stud bolt mountings and four holes for the brake rotor mounting.
For the selection of Hub bearings, Cost, Bearing Life and Load rating and of course weight.

As you can clearly observe from the catalog that as we go for higher bearing dimensions, the bearing weight and load rating (C, C0) increases. And If we wish to go for a higher load rating for the same dimensions of the bearing the cost will significantly increase. So, we should choose one bearing that is a standard piece and satisfies the load rating criteria.
Determination of Forces
We need to also determine the kind of loads the hub will be subjected to during its operation. That will help us to design the shape and profile of the hub and will also give us Boundary Conditions for FEA analysis of the Hub.
[ Caution: These are my personal calculations based on my knowledge and experience, feel free to correct me! ]
Radial Forces
For determining the boundary condition, we can take the extreme condition of the situation when the buggy lands on a single wheel after jumping from a ramp. In the extreme most case it might come to a sudden stop. From the videos of the BAJA SAEINDIA 2017 season, such a situation happened on the suspension and traction track on the rocks. If the buggy lifts off and land in full speed during rock-travel in S&T event or during multiple consecutive high bumps on the track. Also, during the endurance race, the vehicle and therefore the hub might face such loading conditions.
This is a case of impact loading. So, to determine the force, we need initial and final momentum and we can easily obtain the momentum of the vehicle.
Let's believe in the sincerity of the driver that he won't keep the vehicle in full speed while approaching the obstacles. But, in the middle of the heat of the endurance race, we can expect a shallow jump at the max speed of 60 Kmph. We assumed that the vehicle lands on an obstacle (let's say a rock) and comes to a sudden stop. The landing angle we can take to be equal to 45 degrees, but that doesn't really matter as the angle will have effect on the resolution of the loads and as these forces are radial in nature. As the hub will be rotating, so it can act in any direction.
The time of impact/contact is an important quantity. As it will have a direct impact on the magnitude of forces. as F=dp/dt.
To determine dt, we assume a Spring mass system with the tire as the spring. Here, if you imagine the motion in slow motion, the contact will start when the tire touches the obstacle/rock, Momentum transfer will start from this moment. Then the tire compresses to the maximum level, then it removes the compression moving towards the initial position, and when it reaches the initial position the contact will end. So the whole momentum transfer happens in this time frame, that amounts to T/2, where T is the time period of oscillation in the spring-mass damper system. Mass here is that of the whole vehicle as we assume that vehicle lands on one wheel.
The tire stiffness depends on tire properties as well as air pressure. As we don't have information available for the ATV tires that we use, for an estimate we can take the value from normal passenger vehicle tire.
from,

we get dt=T/2
Substituting the values we get the radial forces acting on the hub in the extreme case.
During Braking:
During braking, the brake bolts will be fixed and the tire will exert braking force through stud bolts, or we can consider the opposite case, that the stud bolts are relatively fixed and braking force is exerted by the brake disc through brake disc mounting bolts.
[ If you are finding it difficult to understand how this forces act, you should imagine the relative motion of the components assuming the hub to be flexible, and imagine how the hub will deflect. That will give you insights and a feel on how these forces act. ]
Brake forces are easy to calculate. We have learned this during Machine Design Course or we can get it from the Brake Dept.
Axial Forces:
Imagine your car skidding during the drift, that contributes to axial forces in the hub. That equals to the traction/friction (mu*N, mu=friction coefficient) at the wheel.
Another extreme case can be while overcoming log of woods or approaching them at an angle. That will cause the force in a radial direction and axial direction. The forces here can be calculated in a similar way to how we calculated earlier in the jump and land on single wheel case. And resolve that forces in radial and axial direction. We can get maximum axial force condition on the wheel hub.
Design Optimization
The approach I used is to determine the forces, apply those forces in a Topology Optimization software ( Altair INSPIRE), and get a sense/feel of what an optimized topology should look like. Also, the concepts learned in Solid Mechanics came to my aid to progress quickly towards the optimized shape. The following image shows the results of such optimization at various mass reduction percentages.

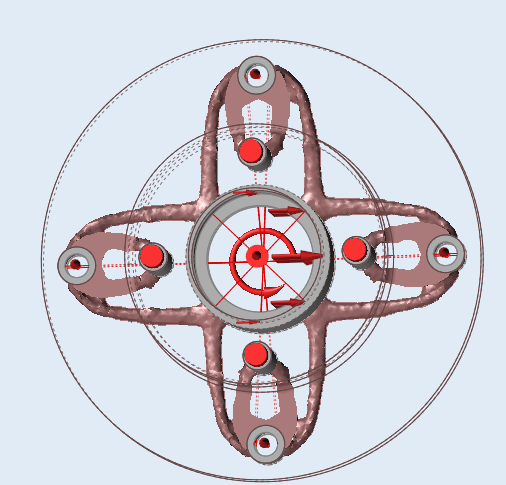
I observed that in the second figure, that at the ridges from the wheel rim mount pints to the intersection points of y=|x| line emerged, and it tried to connect the rotor mounting points from the wheel mounting points. In the subsequent iterations, I decided to move brake mount points on the y=|x| line to remove that unnecessary material.
Interpreting the results:
Why this shape emerged can be easily understood, as all the flanges will be under bending loads, so for stiffness in bending the 2nd moment of area of the cross-section must be high, therefore the ridges went to meet the y=|x| line from the wheel mounting points. Also, we can see that near the bearing/axle the bending moments/loads will be high, as M= P*l, so the moment of area, I should be higher near the axle and can be lower as the radius increases. To achieve it, I gradually increased the thickness of the flange towards bearings and also gradually expanded them to cover the thickness of the bearings. Then iterating with the thickness and width with ANSYS FEA Analysis, we arrive at the optimum design of the wheel hub.
CAD Modelling
For designing these hubs in CAD software:
Utilize Shaft (in CATIA) or Revolve ( Solidworks) feature to design the cross-section of the beam and vary the thickness of the flange properly.
For cutting out material in between, use Pockets/Cut Extrude/Hole Wizard to create holes for mounting rim and brake-disc.
Refine the geometry with chamfers and fillets to reduce stress concentrations.
Comments